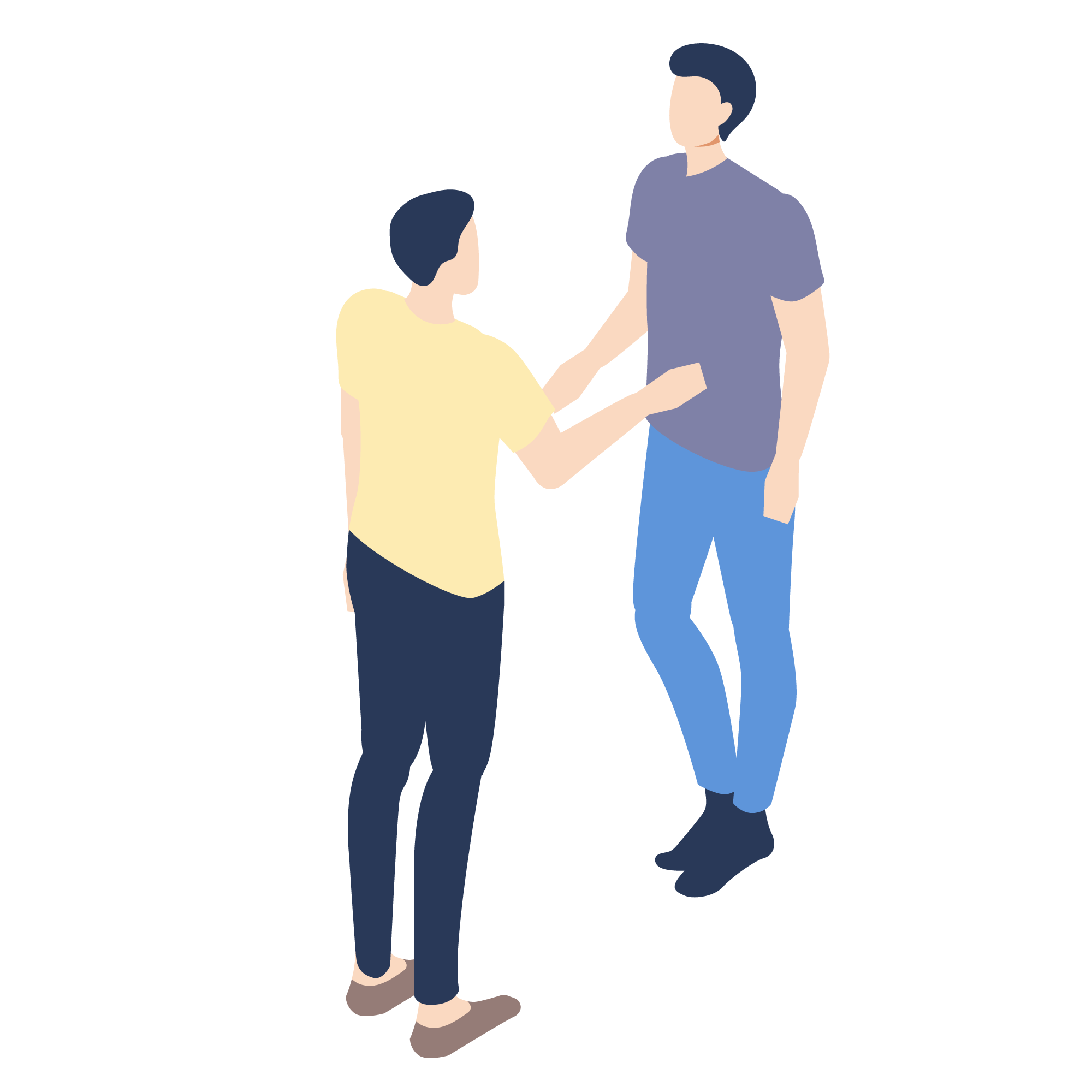
About Us
-
“Skanda” provides Assurance goes beyond testing and inspection to look at the underlying elements that make a company and its products successful.
-
“Skanda” delivers confidence and total peace of mind that customer operating procedures, systems and people are functioning properly to stretches a competitive advantage in the marketplace.
-
Our extensive services provide insight into every aspect of operations, allowing client to make informed decisions about his business.
-
Our training services ensures the workforce competencies are current and relevant.
-
“Skanda” brings their knowledge to clients on assessing overall performance, the quality and productivity of pharma industry, identifying and mitigating risks, streamlining manufacturing processes, and so much more.
Services
-
Prepare and manage required SOPs for cGMP compliance
-
Train staff in cGMP policies and compliance
-
Prepare and execute Quality Agreements with contract manufacturers (CMOs)
-
Serve as the Release Authority on behalf of the client


cGMP Auditing
-
Assess and consult on level of compliance of manufacturers
-
Provide written gap analysis
-
Proposing compliance improvement opportunities
-
Define required CAPA
-
Establish missing or incomplete quality systems
-
Prepare needed SOPs
-
Train both manufacturing and quality unit staff
Manufacturing Operations
-
Review and recommend opportunities for improvement of batch records and other operations documentation to improve shop floor and QA release efficiency
-
Advise on suitability of facilities for manufacturing to ensure GMP compliance
-
Provide an organizational strategy for conducting and reporting manufacturing and quality failure investigations to assess root cause and define corrective action and preventative actions
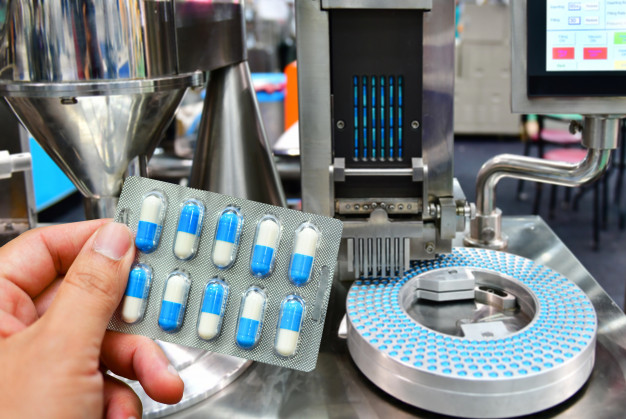
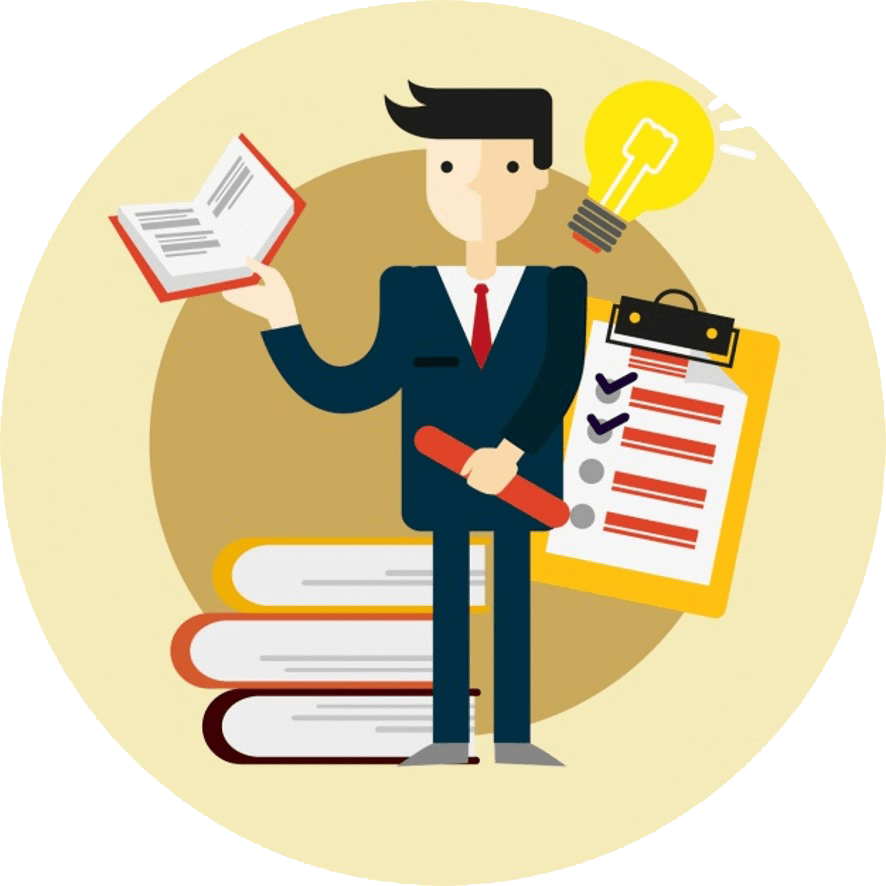
Validation
-
Help create the critical process parameter analysis experimental plan to be consistent with Quality by Design (QbD) concepts
-
Draft the process validation protocol to be consistent with QbD concepts
-
Help organize the process validation plan or validation data and the water validation systems to give the customers to comply with the stringent global standards.
Preparation for Agency Inspection
Train Quality staff to manage a regulatory authority inspection, including:
-
Train SMEs on proper procedures for responding to investigator questions
-
Set up documentation “war room”
-
Ensure all previously identified CAPA are complete
-
Perform final housekeeping inspection to ensure a facility is fully prepared
-
Organize daily de-briefing and assignment of follow-up duties
-
Advise on response to all inspection observations
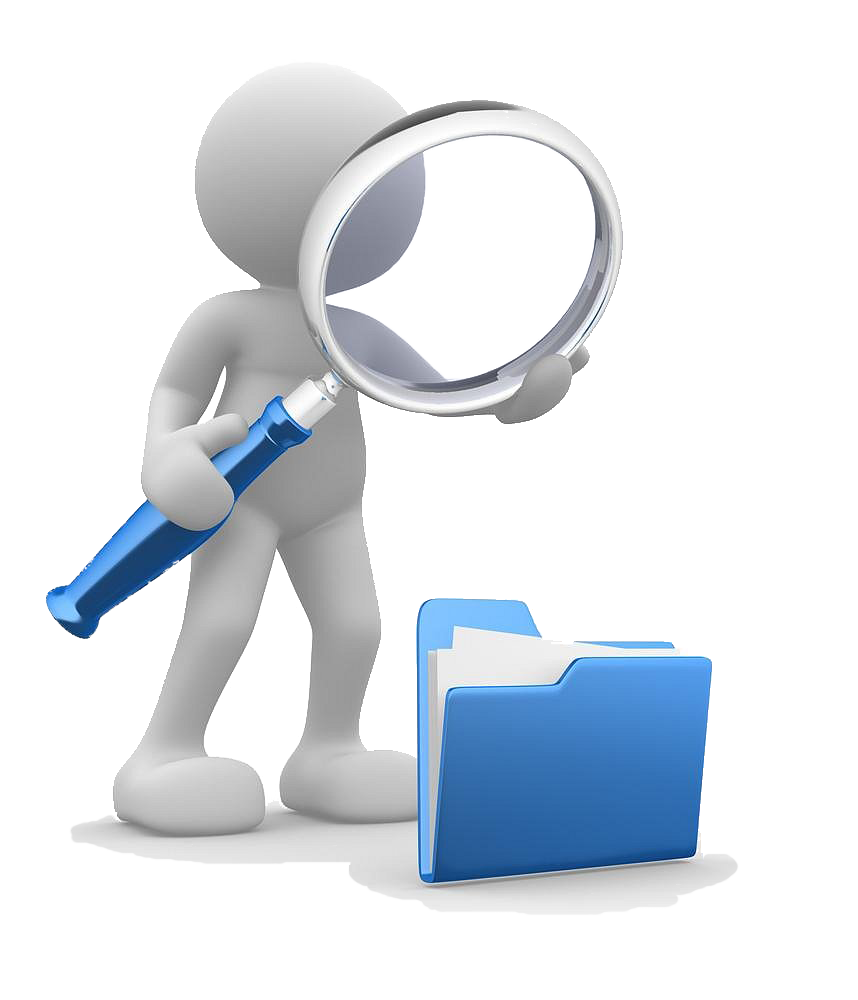